Inconel® Alloys
Specialist Inconel® Alloys from NeoNickel display high levels of oxidation resistance and corrosion resistance when exposed to high temperatures.
Based on a nickel-chromium alloy with added aluminium, these alloys have properties which make them perfect for use in the heat-treating industry.
What Are Inconel® Alloys?
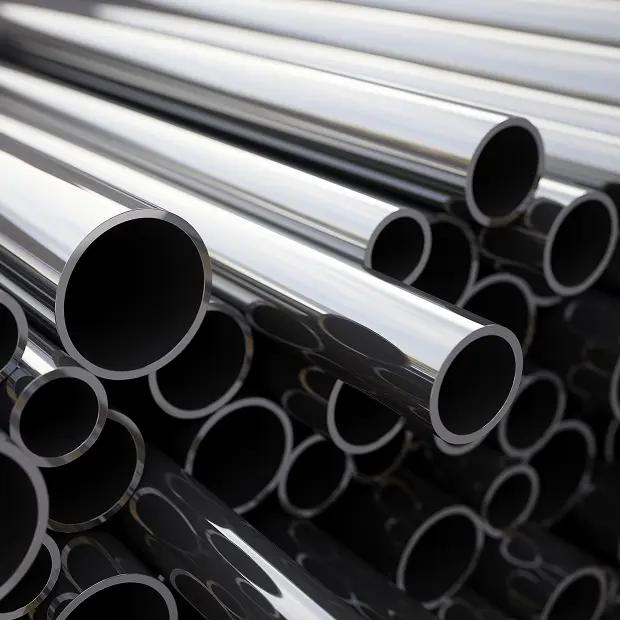
What Are Inconel® Alloys?
Inconel® alloys are nickel-based alloys, enriched with chromium and iron. Engineered to deliver exceptional performance, they are renowned for their robustness in demanding environments.
The Importance of Trademark
‘Inconel®’ is more than just a name; it’s a registered trademark of Special Metals Corporation. This means when you purchase Inconel®, you’re buying a product specifically manufactured and branded by this company. The Inconel® alloys provided by NeoNickel are of the highest quality and authenticity, meeting the most stringent industry standards for reliability and performance. View our quality approvals here.
Types of Inconel® Alloys
NeoNickel supplies a comprehensive range of corrosion-resistant Inconel® alloys designed for extreme chemical environments:
What is Special about Inconel®?
When it comes to selecting materials that offer unmatched durability and performance in extreme conditions, Inconel® alloys emerge as the superior choice with their:
High-Temperature Stability
Can maintain their structural integrity at extreme temperatures.Inconel Alloys
Strength and Durability
Ideal for heavy-duty applications, because of their high tensile strength and resistance to stress-corrosion cracking.
Resistance to Extreme Pressure
This trait is particularly beneficial in deep-sea and aerospace applications, where pressure conditions can be incredibly intense.
Low Thermal Expansion
Inconel® alloys have a lower rate of thermal expansion compared to many other materials; they do not change shape significantly when exposed to temperature variations, ensuring dimensional stability in precision applications.
Corrosion Resistance
Inconel® alloys exhibit excellent resistance to oxidation and corrosion due to the presence of chromium, particularly valuable in environments exposed to extreme weather, saltwater and corrosive chemicals.
Ease of Fabrication
Despite their robustness, Inconel® alloys can be engineered and shaped to meet specific requirements.
Versatility Across Industries
Inconel®’s properties make it versatile across various industries.
Inconel® Alloys: Versatile Applications in Various Industries
Inconel® alloys have outstanding resistance to corrosive gases like dry chlorine (Cl2) and hydrogen chloride (HCl). This chemical resistance makes them a top choice in environments where such aggressive substances are prevalent.
Beyond their chemical robustness, Inconel® alloys are engineered to withstand continuous exposure to extreme temperatures and pressures without losing their integrity. This enduring strength, coupled with a notable resistance to creep – the gradual deformation under high stress – makes Inconel® alloys indispensable in the following industries.
NeoNickel: Your Trusted Supplier of Inconel® Alloys
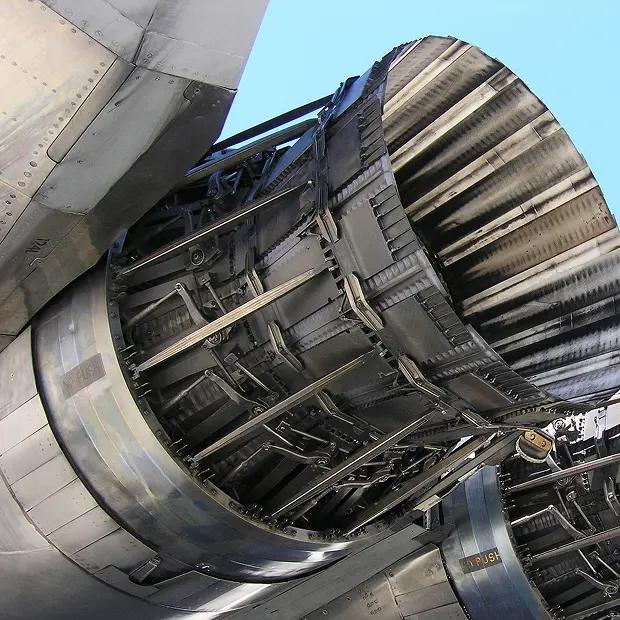
NeoNickel: Your Trusted Supplier of Inconel® Alloys
At NeoNickel, we pride ourselves on offering the highest-quality Inconel® alloys to meet the specific needs of our clients. Our comprehensive range of corrosion-resistant and heat-resistant grades ensures that we have the ideal solution for your application.
Extensive inventory of Inconel® alloys.
Expertise in custom machining and fabrication.
Reliable, on-time delivery for critical projects.
Recent Articles About Inconel® Alloys
Inconel Alloy 625 Vs Inconel Alloy 718
Alloy 625 and Alloy 718, are both nickel alloys, both superalloys and part of the Inconel family of [...] Read more
The Properties of Metals and Alloys & How They Affect Use
Comparing the properties of alloys and pure metals is important when trying to procure materials. In [...] Read more
What is an Alloy Metal? The Beginner’s Guide
An alloy is a mixture of two or more metals. The primary constituent is the base metal and the secon [...] Read more
Frequently Asked Questions
Determining the "strongest" Inconel® alloy can be complex, as the strength of an alloy depends on various factors like temperature, type of stress (tensile, yield, fatigue, etc.) and the specific conditions of use. However, among the Inconel® family, certain alloys are recognised for their exceptional strength characteristics:
Inconel® 718/ Alloy 718: Chosen for its high tensile and yield strength, especially at elevated temperatures. It's widely used in aerospace applications due to its ability to maintain strength under extreme conditions.
Inconel® X-750/ Alloy X-750: Known for its excellent mechanical properties at high temperatures and its resistance to relaxation, making it strong in applications involving thermal cycling.
Inconel® 725/ Alloy X-750: As an evolution of Alloy 625, Alloy 725 is noted for its increased strength, being about twice as strong as annealed Alloy 625 due to its unique composition and heat treatment processes.
The "strongest" alloy for a given application will depend on the specific requirements of that application, including the type of stress it needs to withstand and the environmental conditions it will face. Therefore, it's essential to consider all these factors when selecting an Inconel® alloy for a particular purpose.
When comparing Inconel® and titanium, the question of which is "better" largely depends on the specific application and environment in which the material will be used. Both materials have unique properties that make them suitable for different applications.
Inconel® excels in heat resistance, maintaining strength at high temperatures where other metals falter, making it ideal for applications like jet engines and industrial furnaces. Titanium, while also heat resistant, doesn't match Inconel® in extreme temperatures but offers a superior strength-to-weight ratio, favoured in aerospace and automotive industries for its lightweight yet strong properties.
Both materials are corrosion-resistant, with Inconel® excelling in harsh environments and titanium being particularly resistant to saltwater, making it suitable for marine and medical uses. The choice between Inconel® and titanium ultimately hinges on specific application needs, including temperature tolerance, strength, weight and corrosion resistance.
Inconel®, renowned for its corrosion resistance, exhibits a remarkable ability to resist rusting, even in harsh environments. Its unique composition, primarily consisting of nickel and chromium, forms a protective oxide layer on the surface, which acts as a barrier against oxidation and rust.
While no material can be deemed entirely rustproof in all conditions, Inconel® comes exceptionally close, offering a high level of protection against rust compared to many other metals. Its resilience in preventing rust makes it a dependable choice for applications where durability and longevity are crucial.